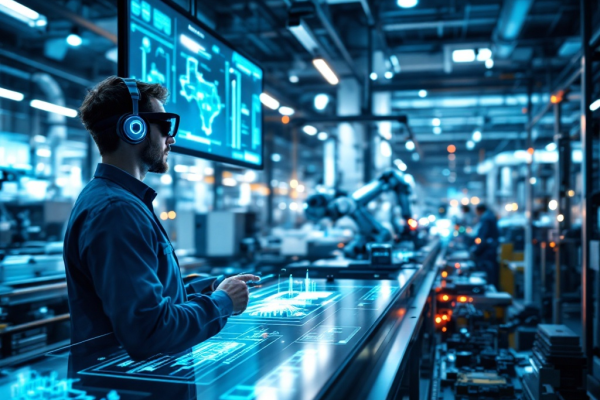
Laser Sensors: How the Industry is Moving Towards a New Wave of Precision
Introduction
Imagine trying to measure the speed of a high-speed conveyor belt or determining the precise location of a machine part down to the micron level. In the past, these tasks required cumbersome mechanical systems or manual intervention. Today, industries are turning to laser sensors—compact, reliable, and incredibly precise devices that revolutionize manufacturing and automation.
From oil refineries in Texas to cutting-edge robotics labs, laser sensors are paving the way for smarter, more efficient industrial processes. In this article, we will explore how these devices work, where they are used, and how they are shaping the future of industry.
How Laser Sensors Work
At the core of every laser sensor is the ability to measure distance, position, or speed by analyzing the interaction of a laser beam with a target object. Unlike traditional measuring tools, laser sensors provide non-contact measurements, making them ideal for fast-moving or delicate components.
1. Time of Flight (ToF) Measurement
A widely used principle in laser sensing, Time of Flight (ToF) relies on measuring how long it takes for a laser pulse to travel to an object and back. Given that the speed of light is constant, the system calculates the exact distance of the object based on the time delay.
Advantages:
- High precision, even for long distances.
- Suitable for logistics, robotics, and industrial automation.
Applications:
- Warehouse management.
- Distance monitoring in self-driving vehicles.
- Smart factory automation.
2. Modulated Light Measurement
Another approach is modulating the laser’s intensity and measuring the phase shift of the reflected light. By comparing the emitted and received waveforms, the system calculates the distance with extreme accuracy.
Advantages:
Works well in indoor environments with reflective surfaces.
Can handle high-speed measurements with minimal errors.
Applications:
- Automated assembly lines.
- Machine vision.
- Semiconductor manufacturing.
3. Triangulation Sensors
Inspired by geodesy, triangulation sensors measure distance by analyzing angles. A laser beam is projected onto the target, and the reflection is captured by a detector. Depending on the target’s distance, the reflected laser spot shifts in position.
Advantages:
- Ideal for high-precision measurement of small objects.
- Reliable in challenging industrial environments.
Applications:
- Microelectronics production.
- CNC machining.
- Medical device manufacturing.
Industrial Applications of Laser Sensors
Laser sensors are used in various industries, each leveraging their precision for different purposes. Here’s a closer look at some of their most impactful applications:
1. Oil and Gas Industry (Texas Focus)
In Texas, the oil and gas sector relies on laser-based LiDAR (Light Detection and Ranging) systems to monitor pipelines, detect leaks, and analyze terrain for drilling operations. Unlike traditional monitoring methods, laser sensors provide real-time data, ensuring safety and efficiency in extraction processes. These sensors also help in detecting structural weaknesses, reducing the risk of spills and environmental hazards.
Additionally, laser sensors are used for flare stack monitoring, ensuring compliance with emissions regulations and improving safety in refineries. Texas, being a major hub for oil and gas, has seen increasing adoption of such laser-based solutions to enhance efficiency and reduce risks.
2. Manufacturing and Quality Control
Factories worldwide use laser sensors for process optimization and quality assurance. In high-speed production lines, these sensors detect microscopic defects in materials, ensuring that every product meets stringent quality standards.
Examples:
- Automotive industry: Laser sensors measure the alignment of vehicle parts with sub-millimeter precision.
- Semiconductor manufacturing: Verifying wafer thickness and detecting imperfections.
- Metal fabrication plants: Laser profiling ensures welds are properly aligned and meet safety regulations.
Laser sensors also contribute to predictive maintenance, where machines equipped with these sensors monitor vibrations and misalignments, preventing costly breakdowns before they occur.
3. Speed Measurement in Industrial Automation
To measure the speed of moving objects, manufacturers use:
Time-of-Flight sensors that take multiple distance readings over a short interval.
Light barrier systems, where an object passes between two laser points, and the time between interruptions is recorded.
Doppler Effect sensors, which detect frequency shifts caused by moving objects. This method provides unparalleled accuracy, making it ideal for high-precision engineering.
In Texas-based aerospace manufacturing, speed measurement plays a critical role in testing jet engine components, where precision is crucial for safety and performance.
4. Robotics and Automated Systems
As industries shift towards smart automation, laser sensors become essential for:
Obstacle detection in autonomous robots.
Path planning for warehouse AGVs (Automated Guided Vehicles).
Position tracking in robotic arms for delicate assembly tasks.
One emerging trend is the integration of 3D laser scanning, which allows robots to create a real-time map of their surroundings, improving navigation and object manipulation.
LiDAR: The Future of Industrial Sensing
One of the most groundbreaking technologies in laser sensing is LiDAR (Light Detection and Ranging). This system creates highly detailed 3D maps of environments by emitting laser pulses and measuring their reflections. It is used in:
Self-driving cars (Tesla, Waymo, and other brands rely on LiDAR for navigation).
Construction and mining (LiDAR scans landscapes to plan infrastructure projects).
Warehouse automation (Optimizing storage and movement of goods).
LiDAR in Texas Industries
Texas is a hub for LiDAR adoption, particularly in:
Trucks used in logistics and freight transport.
Smart city projects utilizing LiDAR for traffic management and infrastructure planning.
These implementations are improving safety, efficiency, and sustainability in Texas industries.
Challenges and Future of Laser Sensors
Despite their numerous advantages, laser sensors face certain limitations:
Environmental Sensitivity – Performance can be affected by fog, dust, or reflective surfaces.
Cost – While prices have dropped, high-end LiDAR systems still require significant investment.
Data Processing – The vast amount of data generated by laser sensors requires powerful computing resources.
However, the future looks promising. With advancements in AI-driven analytics, laser sensors will become even smarter, capable of not just measuring but interpreting the data they collect. In Texas, where automation and robotics are booming, laser sensors will be at the forefront of next-generation industrial transformation.
Conclusion
Laser sensors are no longer a futuristic concept—they are shaping industries today. From oil refineries in Texas to automated factories in Silicon Valley, they are ensuring precision, safety, and efficiency across multiple sectors.
With ongoing advancements in LiDAR, AI integration, and miniaturization, laser sensors will become even more cost-effective and widely used. Companies that adopt these technologies will gain a competitive edge, ensuring they stay ahead in the rapidly evolving industrial landscape.
As Texas continues to invest in automation and digital transformation, one thing is certain—laser sensors are here to stay, revolutionizing the way industries operate.