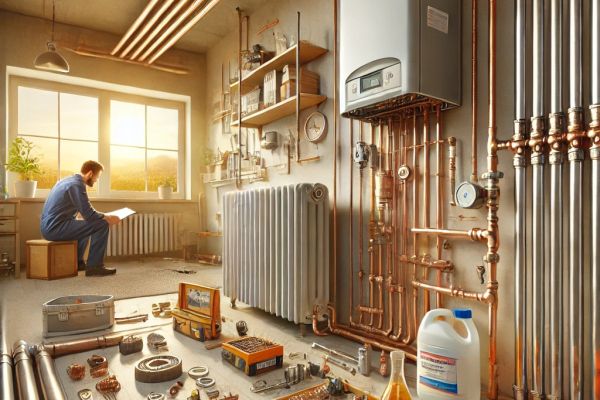
Stop the Rust: How to Protect Heating Systems from Corrosion and Save Your Budget
Introduction
The issue of corrosion in heating systems is especially pressing these days. It’s one thing when a residential boiler unexpectedly breaks down in the middle of winter, but quite another when corrosion forces an entire production line or office complex to shut down. In either case, the damage can be substantial—financial costs for repairs, downtime, lost time, and frayed nerves. Moreover, when corrosion “infects” a heating system, it not only results in repair bills but also reduces the overall efficiency of the system: utility expenses rise, and equipment reliability drops. That’s why many experts and experienced plumbers—even in the scorching state of Texas—are seriously tackling the rust problem and looking for ways to ensure a long service life for building infrastructure.
In this article, we will break down where corrosion comes from, what problems it leads to, and how exactly it can be stopped. We’ll offer practical advice, recommendations, and we’ll also highlight specific nuances of operating heating systems in different regions, including the climatic conditions of Texas.
Causes of Corrosion: Why Metal Gets “Eaten Away” From the Inside
Chemical Composition of the Water
Tap water contains various salts and mineral impurities. In certain regions, it may have a higher iron or sulfur content. When heated, these substances react with the materials in pipes and radiators, contributing to corrosion. For example, water with high levels of dissolved oxygen accelerates oxidation and “gnaws away” at the inner walls of the pipes.
Different Metals in One System
When dissimilar metals are used in the same system—say, steel pipes, copper heat exchangers, and brass fittings—galvanic corrosion can occur. One metal “sacrifices” its ions to another, triggering a reaction that accelerates deterioration. This problem is especially common when improper or low-quality connectors are used, or if there are mistakes in installation.
Poor pH Control
The pH level directly affects the aggressiveness of the water. If the pH drifts outside the recommended range, metals begin to oxidize more quickly. Ideally, a heating system’s pH should be balanced, which can be achieved through specialized chemical treatments and periodic water testing.
Insufficient Maintenance
A heating system that goes years without proper maintenance—where filters aren’t checked, water isn’t replaced or chemically treated, and regular service checks are ignored—faces a significantly higher risk of corrosion. Building owners often overlook their pipework until a serious breakdown happens.
Design Errors
Incorrect flow rates, unwanted water stagnation zones, or improper pressure levels all create ideal conditions for corrosion. When the system is designed from the start with hydrodynamics in mind, it performs more reliably and for a longer period.
The Impact of Climate and What’s Special About Texas
High Temperatures
The higher the water temperature, the more active the chemical reactions. If a heating system is used seasonally (in winter) and remains idle for a long time (in summer), deposits can form in the pipes that accelerate corrosion the next time the system is turned on.
Hard Water
In some parts of Texas, the water can be extremely hard, with elevated levels of calcium and magnesium salts. This leads to scale buildup on the walls of heat exchangers and pipes. Scale, in turn, reduces heat-transfer efficiency and further accelerates corrosion beneath the deposits.
Intermittent Operation
In warmer climates with shorter heating seasons, systems may be switched on and off more frequently. The multiple heating-cooling cycles, combined with dissolved oxygen in the water, can create numerous corrosion hotspots over time.
All of this means that those responsible for designing and operating heating systems in Texas (and in other regions with similar climates) must pay extra attention to preventing corrosion and scale buildup.
The Consequences of Corrosion: Obvious and Hidden Losses
Reduced Equipment Lifespan
Metal literally “eats away” from the inside, forming microcracks that eventually become leaks. As a result, expensive boilers, pipes, and radiators fail well before their advertised service life is up.
Decreased Efficiency
Deposits lining pipe walls interfere with water flow and diminish heat transfer. More energy is needed to achieve the required level of heating, pushing up energy bills.
Increased Risk of Breakdowns
A pipe burst caused by corrosion—whether it’s in a home or at a business—demands an immediate shutdown, replacement of the damaged section, and cleanup of any leaks. All of this leads to unplanned downtime and extra expenses.
Contamination of Heat Transfer Fluid
Rust particles traveling through the system can clog valves, heat exchangers, filters, and other components, resulting in added costs for cleaning and repairs.
Methods of Prevention and Control
High-Quality Water Treatment
This is a key factor. Before water enters a heating circuit, it should be filtered, softened, or treated with the appropriate chemicals (depending on its initial quality). In areas with particularly hard water, such as parts of Texas, using water softeners or phosphate additives helps reduce scale formation.
Regular Diagnostics and Water Analysis
Even a brand-new system that’s only been in operation for a year should undergo periodic water testing to check pH levels, concentrations of iron, copper, and other metals, as well as hardness salts. If any indicators exceed recommended levels, the water chemistry should be corrected with suitable additives.
Use of Specialized Materials
Manufacturers now offer stainless steel pipes, alloyed metals, polymer pipes, and metal-polymer lines. While these may cost more up front, they are far more corrosion-resistant, ultimately saving money in the long run.
Monitoring Connections and “Electrical Compatibility”
To avoid galvanic corrosion, it’s best to use compatible materials and special dielectric fittings between dissimilar metals. If a system already includes both steel and copper, be sure to check for electrical leaks and proper installation of fittings and expansion joints.
Protective Coatings and Corrosion Inhibitors
Chemical inhibitors form a thin film on pipe walls that hinders direct interaction between metal and corrosive substances in the water. These chemicals are added to the system carefully to avoid unwanted side effects (like foaming).
Proper System Design
During the design and installation phases, consider how water circulates and where “dead zones” might form. Even temperature distribution and the avoidance of stagnant areas will significantly slow corrosion.
Practical Examples
A Residential Home in an Austin, Texas Suburb
The owner complained about ongoing pipe noise and rusty stains on towel warmers. A thorough inspection revealed below-normal pH levels and high iron content in the supply water. After installing a filtration system and routinely adjusting water chemistry, corrosion decreased significantly, the noise subsided, and the towel warmers stopped showing rust-like deposits.
A Commercial Office Complex in Dallas
The building’s modern heating system used a combination of copper and steel components. After two years of operation, early signs of galvanic corrosion appeared on the fittings. Specialists installed dielectric connectors and implemented a regular water-testing schedule. This halted the corrosion process and averted the costly replacement of pipes.
Operation and Maintenance: The Key to System Longevity
Timely Flushing
If tests show high levels of rust or deposits, flushing the system with specialized solutions can dissolve scale and clean the internal surfaces of the pipes.
Regular Inspections
Check the condition of connections, fittings, and seals. Corrosion often starts covertly, with its initial signs manifesting as microcracks or whitish, salty deposits around joints.
Maintaining the Correct Temperature
Constantly running a boiler on its highest setting (especially in homes that attempt to “regulate” indoor temperature solely by cranking the boiler) can lead to rapid water evaporation and increased salt concentration. An optimal operating mode prevents system overloads and extends equipment life.
System Storage in the Off-Season
If the system is completely shut down in summer, consider draining the water or, on the contrary, filling it with a specially prepared solution rather than leaving empty pipes in contact with oxygen. Proper off-season conservation is crucial in regions with a short heating season.
The Importance of Prevention and Its Economic Impact
Plumbing professionals often say, “It’s easier and cheaper to prevent a problem than to fix it.” This principle applies perfectly to corrosion prevention. Good upkeep and preventive measures cost far less than dealing with the aftermath of a major breakdown. Imagine a large business center where a pipe in the heating loop bursts due to corrosion. Water floods offices, damaging equipment and possibly cutting power. The resulting losses can be enormous—far more than the annual expense of preventive maintenance and replacing vulnerable parts.
Additionally, regular monitoring of the system’s condition keeps everything running efficiently, saving energy and other resources. By cutting down on energy use and avoiding emergency shutdowns, building owners see real cost savings.
Conclusion: Keeping Corrosion Under Control
Corrosion is a serious threat to any heating system, whether it’s in an apartment, a private home, or a large business complex. It can lead to breakdowns, downtime, and major financial losses. However, there’s a wide arsenal of tools and methods available today to “tame” rust and stop its destructive impact.
Key Takeaways:
- Timely Water Treatment – filters, softeners, and chemicals.
- Smart Design – careful handling of dissimilar metals, proper flow rates, avoiding stagnant zones.
- Constant Monitoring – regular checks of pH levels, visual inspections for corrosion, and checks of fittings and seals.
- Thoughtful Operation – maintaining an optimal temperature, properly switching the system off or conserving it between seasons, and performing routine maintenance.
A comprehensive approach is the key to long, trouble-free operation of your heating system—whether you own a cozy ranch in Texas or are responsible for a sprawling business center elsewhere in the country. The earlier you address corrosion prevention, the fewer problems and costs you’ll face down the road. Investment in anti-corrosion measures invariably pays off, whether in residential or industrial settings.
For peace of mind and confidence in every weld and every meter of pipe, consult with professional plumbers and system engineers. Experts can help you select the best solution and ensure that every stage—from design to system startup—meets the highest standards of quality and safety.
The bottom line is that corrosion never sleeps, but neither do we, the experienced plumbing professionals. By using modern technologies, conducting regular maintenance, and performing ongoing tests, we can give your infrastructure a long life and save you from unwanted stress. With such a plan in place, any building—whether a home in Texas or a manufacturing plant up north—will stay warm, safe, and free from costly repair bills.